Life Long Project
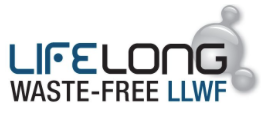
- Obiettivi
- Risultati attesi
- Problema ambientale affrontato
- Azioni
- Risultati raggiunti
- Dissemination
- Avanzamento tecnico
- Download
Gli obiettivi del progetto sono la riduzione dei rifiuti, la riduzione dell'uso di sostanze chimiche e il contenimento delle emissioni di CO2 attraverso un innovativo metodo di deumidificazione a tolleranza minima (-5%) durante la produzione del PVC.
L'attuale metodologia di deumidificazione del PVC sia durante il processo di composizione che di estrusione è inadeguata.
L'umidità residua durante le fasi di preparazione e produzione del PVC crea fenomeni di degradazione idrolitica catalizzata dalle forze termo-meccaniche, che si manifestano attraverso la presenza di imperfezioni (doppi legami, gruppi carbonilici e idroperossidi) e la formazione di sequenze di doppi legami coniugati. Durante la fase di estrusione, quindi, il materiale da trattare assorbe ulteriore umidità, che può comportare ulteriori scarti di lavorazione, fermi macchina e manutenzione straordinaria.
Un rimedio consiste nell'uso di prodotti chimici stabilizzanti e plastificanti in quantità superiore al 30% rispetto alla situazione normalizzata, cioè senza umidità durante il ciclo. Durante questa fase, la produzione del granulo può essere parzialmente compromessa dalla formazione di rifiuti (15% di prodotti trattati in eccesso). Inoltre, in presenza di umidità, anche minima, gli effetti della degradazione sono ancora presenti, causando ulteriori scarti che, nel caso di materiali destinati ad uso biomedico, possono raggiungere un ulteriore 10%.
L'introduzione di un innovativo modo di misurare in tempo reale il contenuto di umidità dei materiali e di personalizzare il trattamento demoisturizzante caso per caso, rappresenterebbe un enorme vantaggio, in grado di annullare completamente la necessità di un overtreatment e le problematiche ad esso connesse.
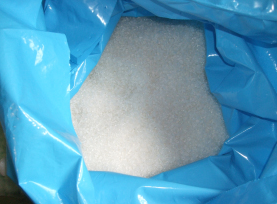
L'umidità residua durante le fasi di preparazione e produzione del PVC crea fenomeni di degradazione idrolitica catalizzata dalle forze termo-meccaniche, che si manifestano attraverso la presenza di imperfezioni (doppi legami, gruppi carbonilici e idroperossidi) e la formazione di sequenze di doppi legami coniugati. Durante la fase di estrusione, quindi, il materiale da trattare assorbe ulteriore umidità, che può comportare ulteriori scarti di lavorazione, fermi macchina e manutenzione straordinaria.
Un rimedio consiste nell'uso di prodotti chimici stabilizzanti e plastificanti in quantità superiore al 30% rispetto alla situazione normalizzata, cioè senza umidità durante il ciclo. Durante questa fase, la produzione del granulo può essere parzialmente compromessa dalla formazione di rifiuti (15% di prodotti trattati in eccesso). Inoltre, in presenza di umidità, anche minima, gli effetti della degradazione sono ancora presenti, causando ulteriori scarti che, nel caso di materiali destinati ad uso biomedico, possono raggiungere un ulteriore 10%.
L'introduzione di un innovativo modo di misurare in tempo reale il contenuto di umidità dei materiali e di personalizzare il trattamento demoisturizzante caso per caso, rappresenterebbe un enorme vantaggio, in grado di annullare completamente la necessità di un overtreatment e le problematiche ad esso connesse.
Numerosi sono i risultati attesi, che riguardano il risparmio energetico, l'uso intelligente delle materie prime, la minimizzazione della produzione di rifiuti, anche se riciclabili, il ridotto utilizzo di sostanze chimiche e l'ottimizzazione del ciclo produttivo:
- Riduzione delle emissioni di CO2: Il nuovo sistema, regolando immediatamente l'umidità contenuta nel materiale, sarà in grado di risparmiare l'energia termica necessaria per la deumidificazione puntando ad un risparmio del 50% di emissioni in CO2, equivalenti a 280 ton/anno.
- Rimozione degli scarti di produzione: L'errata ed inefficiente deumidificazione provoca danni irreversibili alle materie prime, ai semilavorati e ai prodotti finiti, creando inefficienze e produzione di rifiuti (285 ton/anno) che, durante il riciclo, consumano energia creando intolleranti emissioni di CO2 (circa 116 ton/anno).
- Risparmio e recupero di materie prime: Il ciclo produttivo ridisegnato consentirà di spessorare con precisione il film con tolleranza micrometrica, riducendo l'utilizzo di materie prime. Il controllo dell'umidità elimina il rischio di trasformare il materiale non idoneo, recuperandolo intatto prima della trasformazione. Il pieno recupero dei materiali di scarto, perfettamente compatibili con il materiale vergine, consentirà inoltre di risparmiare materie prime ed emissioni di CO2 (97 ton/anno).
- Minore uso e spreco di additivi: Gli additivi (plastificanti, ritardanti di fiamma, catalizzatori in genere) sono i primi ad essere volatilizzati durante l'essiccazione in caso di eccessiva deumidificazione e questo richiede un uso sovrabbondante. Un'umidità equilibrata dei materiali consentirà di utilizzare la quantità strettamente necessaria, consentendo una percentuale media di riduzione del 30%.
- Controllo costante e gestione ottimale della qualità dei prodotti: Il controllo costante dell'umidità e del calore del materiale consente di definire preventivamente i parametri fondamentali del processo, offrendo protezione in caso di condizioni atmosferiche (variazioni di temperatura e umidità esterna).
- Riduzione delle emissioni di CO2: Il nuovo sistema, regolando immediatamente l'umidità contenuta nel materiale, sarà in grado di risparmiare l'energia termica necessaria per la deumidificazione puntando ad un risparmio del 50% di emissioni in CO2, equivalenti a 280 ton/anno.
- Rimozione degli scarti di produzione: L'errata ed inefficiente deumidificazione provoca danni irreversibili alle materie prime, ai semilavorati e ai prodotti finiti, creando inefficienze e produzione di rifiuti (285 ton/anno) che, durante il riciclo, consumano energia creando intolleranti emissioni di CO2 (circa 116 ton/anno).
- Risparmio e recupero di materie prime: Il ciclo produttivo ridisegnato consentirà di spessorare con precisione il film con tolleranza micrometrica, riducendo l'utilizzo di materie prime. Il controllo dell'umidità elimina il rischio di trasformare il materiale non idoneo, recuperandolo intatto prima della trasformazione. Il pieno recupero dei materiali di scarto, perfettamente compatibili con il materiale vergine, consentirà inoltre di risparmiare materie prime ed emissioni di CO2 (97 ton/anno).
- Minore uso e spreco di additivi: Gli additivi (plastificanti, ritardanti di fiamma, catalizzatori in genere) sono i primi ad essere volatilizzati durante l'essiccazione in caso di eccessiva deumidificazione e questo richiede un uso sovrabbondante. Un'umidità equilibrata dei materiali consentirà di utilizzare la quantità strettamente necessaria, consentendo una percentuale media di riduzione del 30%.
- Controllo costante e gestione ottimale della qualità dei prodotti: Il controllo costante dell'umidità e del calore del materiale consente di definire preventivamente i parametri fondamentali del processo, offrendo protezione in caso di condizioni atmosferiche (variazioni di temperatura e umidità esterna).
Il problema ambientale affrontato è la presenza di umidità nei polimeri e nei tecnopolimeri riciclati, che ha effetti negativi sulla loro lavorabilità ed è responsabile della necessità di trattamenti multipli e della generazione di rifiuti o, viceversa, della necessità di utilizzare additivi plastificanti per cercare di recuperarne parte delle proprietà.
La dimensione del problema ambientale è enorme e crescente, in quanto è enorme il mercato attuale e l'uso della plastica e considerando che quando si ricicla il polimero, prima del ritrattamento, è obbligatorio ridurre il contenuto di acqua al di sotto di 100 ppm, altrimenti i materiali ritrattati saranno macchiati da aree lattiginose, viziati da bolle e presenteranno proprietà meccaniche e durata molto inferiori: rimarrebbero rifiuti.
Per questo motivo, negli ultimi decenni sono stati utilizzati sistemi di disidratazione sempre più avanzati, che utilizzano aria calda, campi elettromagnetici, vuoto, ma tutti caratterizzati da un'efficienza energetica estremamente bassa e dalla generazione di prodotti trattati in eccesso, con effetti dannosi su alcune parti dei materiali riciclati o dei granuli che sono direttamente esposti all'azione più intensa del calore o del campo elettromagnetico.
I materiali trattati presentano problemi di rilavorazione, in particolare per quanto riguarda la perdita di viscosità e l'ingiallimento, che costringono i produttori ad aggiungere agenti plastificanti per compensare questa situazione, che è una delle principali fonti di inquinamento per i polimeri. Inoltre, questo recupero di materiali trattati in modo eccessivo implica l'utilizzo di nuovi materiali e di maggiore energia nel loro ritrattamento.
L'introduzione di un metodo innovativo per misurare in tempo reale il contenuto di umidità dei materiali e per personalizzare il trattamento demoisturizzante caso per caso, evitando l'utilizzo di parametri di lavorazione grezzi durante la deumidificazione, rappresenterebbe un enorme vantaggio, in grado di annullare completamente la necessità di un overtreatment e le relative problematiche.
La dimensione del problema ambientale è enorme e crescente, in quanto è enorme il mercato attuale e l'uso della plastica e considerando che quando si ricicla il polimero, prima del ritrattamento, è obbligatorio ridurre il contenuto di acqua al di sotto di 100 ppm, altrimenti i materiali ritrattati saranno macchiati da aree lattiginose, viziati da bolle e presenteranno proprietà meccaniche e durata molto inferiori: rimarrebbero rifiuti.
Per questo motivo, negli ultimi decenni sono stati utilizzati sistemi di disidratazione sempre più avanzati, che utilizzano aria calda, campi elettromagnetici, vuoto, ma tutti caratterizzati da un'efficienza energetica estremamente bassa e dalla generazione di prodotti trattati in eccesso, con effetti dannosi su alcune parti dei materiali riciclati o dei granuli che sono direttamente esposti all'azione più intensa del calore o del campo elettromagnetico.
I materiali trattati presentano problemi di rilavorazione, in particolare per quanto riguarda la perdita di viscosità e l'ingiallimento, che costringono i produttori ad aggiungere agenti plastificanti per compensare questa situazione, che è una delle principali fonti di inquinamento per i polimeri. Inoltre, questo recupero di materiali trattati in modo eccessivo implica l'utilizzo di nuovi materiali e di maggiore energia nel loro ritrattamento.
L'introduzione di un metodo innovativo per misurare in tempo reale il contenuto di umidità dei materiali e per personalizzare il trattamento demoisturizzante caso per caso, evitando l'utilizzo di parametri di lavorazione grezzi durante la deumidificazione, rappresenterebbe un enorme vantaggio, in grado di annullare completamente la necessità di un overtreatment e le relative problematiche.
Per raggiungere gli obiettivi del progetto, affrontare il problema ambientale e migliorare lo stato dell'arte, sono necessarie le seguenti azioni:
- Studio e progettazione del corpo di transito della materia prima, con posizionamento dei relativi sensori;
- Studio, progettazione e costruzione di un sensore di umidità per il prodotto, operante a temperatura ambiente (ingresso) e ad alta temperatura (uscita) e relativa taratura con carichi noti;
- Studio e progettazione di un software per la gestione dei parametri con memoria statica per le preimpostazioni standard;
- Costruzione e montaggio dei componenti progettati e produzione di un prototipo demo funzionale;
- Test di funzionalità dei sensori di registrazione per la variazione del flusso di materiale;
- fDefinizione di un ciclo di lavoro standard (un ciclo per ogni tipo di materia prima utilizzata);
- Analisi dei guasti riscontrati e modifiche ai piani originali e ai componenti prototipali;.
- Bilancio di massa ed energetico del nuovo deumidificatore, da confrontare con gli attuali sistemi similari.
Il risultato principale è un impianto pilota di disidratazione funzionante, comprendente sensori, sistemi di trasporto e unità di disidratazione: costi e prodotti si sono dimostrati compatibili con una produzione industriale, consentendo importanti benefici ambientali ed economici.
RISULTATI AMBIENTALI
Numerosi sono i risultati ambientali, che riguardano il risparmio energetico, l'uso intelligente delle materie prime, la minimizzazione della produzione di rifiuti, anche se in parte riciclabili, un ridotto utilizzo di sostanze chimiche e l'ottimizzazione del ciclo produttivo:
- Il nuovo sistema è in grado di regolare immediatamente l'umidità contenuta nel materiale e quindi di risparmiare la maggior parte dell'energia termica necessaria per la deumidificazione, permettendo di utilizzare solo l'energia strettamente necessaria per raggiungere l'obiettivo di deumidificazione e sistemi in gran parte a minor consumo di quelli attuali, consentendo così riduzioni misurate tra il 55 e il 60% delle emissioni totali in relazione al tipo di materia prima lavorata, cioè fino a 400 tonnellate/anno di CO2 con l'impianto pilota per il progetto risparmiato.
- Le azioni di deumidificazione errate o inefficaci provocano danni irreversibili alle qualità intrinseche delle materie prime che vengono trasposte come tali anche nel prodotto finito dove verranno mappate, causando in ogni caso sprechi di prodotto. La quantità di rifiuti non è mai inferiore alle 285-300 ton/anno in ottica aziendale per il solo overtreatment dei materiali con conseguenti emissioni anomale di CO2 pari a 116 ton/anno, che verranno evitate se i rifiuti verranno eliminati. All'interno del progetto si possono risparmiare circa 28-30 tonnellate all'anno di scarti di produzione, che possono diventare 45-50 tonnellate considerando i problemi spesso creati dall'umidità dei materiali durante l'estrusione e quindi quando la miscela secca viene trasformata in materiale gelificato. In quest'ultimo caso si possono risparmiare altre 20 tonnellate/anno di emissioni di CO2. Quindi, circa il 25% dei rifiuti, cioè 50 tonnellate/anno, potranno non essere generati sulle 200 tonnellate/anno trattate dall'impianto pilota.
- Per quanto riguarda i consumi energetici, si può dire che il nuovo sistema ha raggiunto risultati importanti consumando solo 30 kj/kg per l'unità disidratante, non presente nel processo tradizionale (rif. 1000kg/giorno di materiale trattato). Questi ultimi dati devono essere confrontati con i 1900 kj/kg necessari per riciclare 150 kg di rifiuti al giorno prodotti senza controllo dell'umidità. Inoltre, anche se sono state aggiunte alcune fasi di processo, l'intero processo ha migliori prestazioni consumando solo 0,14285 Kwh/kg invece di 0,158 Kwh/kg del processo tradizionale senza unità di disidratazione.
- Il controllo dell'umidità a monte della granulazione può eliminare il rischio di trasformazione di materiale inadatto, recuperandolo integro prima della trasformazione e permettendo di risparmiare materie prime. Il nuovo metodo può così consentire il pieno recupero dei rifiuti rendendoli perfettamente compatibili con il materiale vergine, grazie alla possibilità di omogeneizzare il gradiente dell'acqua con il relativo controllo di viscosità.
- Meno sprechi di additivi: gli additivi (stabilizzanti, lubrificanti, plastificanti, ritardanti di fiamma, catalizzatori in genere) sono i primi ad essere volatilizzati per problemi di essiccazione in caso di eccessiva deumidificazione e richiedono quindi un uso sovrabbondante e prudente. L'umidità equilibrata dei materiali permette di utilizzare solo la quantità strettamente necessaria di additivi. Diverse prove con miscele diverse hanno dimostrato una riduzione percentuale media del 30% nell'uso di additivi chimici, ottenendo prodotti di qualità perfetta con una grande omogeneità di granuli (deviazione standard di umidità: 1%). Considerando che per kg di materiale trattato in media 0,65 kg sono resine principali e 0,35 kg sono additivi e che 0,015 kg di questi ultimi sono additivi che possono essere salvati con il progetto fino al 35-40% (30% in media) ottenere 900 kg di utilizzo di additivi chimici risparmiati all'anno solo con l'impianto pilota in media.
RISULTATI ECONOMICO
L'approccio proposto è più economico di quello attuale. I principali risultati economici riguardano il valore economico diretto generato (circa il +10% stimato) raggiunto principalmente grazie alla riduzione dei costi energetici e all'aumento della produttività (meno sprechi) e dell'immagine aziendale sul mercato. Il minor costo di produzione è attestato a circa il 9%; considerando il miglioramento dell'immagine aziendale che influisce sul prezzo di vendita si può stimare un 10% di valore economico aggiunto.
RISULTATI AMBIENTALI
Numerosi sono i risultati ambientali, che riguardano il risparmio energetico, l'uso intelligente delle materie prime, la minimizzazione della produzione di rifiuti, anche se in parte riciclabili, un ridotto utilizzo di sostanze chimiche e l'ottimizzazione del ciclo produttivo:
- Il nuovo sistema è in grado di regolare immediatamente l'umidità contenuta nel materiale e quindi di risparmiare la maggior parte dell'energia termica necessaria per la deumidificazione, permettendo di utilizzare solo l'energia strettamente necessaria per raggiungere l'obiettivo di deumidificazione e sistemi in gran parte a minor consumo di quelli attuali, consentendo così riduzioni misurate tra il 55 e il 60% delle emissioni totali in relazione al tipo di materia prima lavorata, cioè fino a 400 tonnellate/anno di CO2 con l'impianto pilota per il progetto risparmiato.
- Le azioni di deumidificazione errate o inefficaci provocano danni irreversibili alle qualità intrinseche delle materie prime che vengono trasposte come tali anche nel prodotto finito dove verranno mappate, causando in ogni caso sprechi di prodotto. La quantità di rifiuti non è mai inferiore alle 285-300 ton/anno in ottica aziendale per il solo overtreatment dei materiali con conseguenti emissioni anomale di CO2 pari a 116 ton/anno, che verranno evitate se i rifiuti verranno eliminati. All'interno del progetto si possono risparmiare circa 28-30 tonnellate all'anno di scarti di produzione, che possono diventare 45-50 tonnellate considerando i problemi spesso creati dall'umidità dei materiali durante l'estrusione e quindi quando la miscela secca viene trasformata in materiale gelificato. In quest'ultimo caso si possono risparmiare altre 20 tonnellate/anno di emissioni di CO2. Quindi, circa il 25% dei rifiuti, cioè 50 tonnellate/anno, potranno non essere generati sulle 200 tonnellate/anno trattate dall'impianto pilota.
- Per quanto riguarda i consumi energetici, si può dire che il nuovo sistema ha raggiunto risultati importanti consumando solo 30 kj/kg per l'unità disidratante, non presente nel processo tradizionale (rif. 1000kg/giorno di materiale trattato). Questi ultimi dati devono essere confrontati con i 1900 kj/kg necessari per riciclare 150 kg di rifiuti al giorno prodotti senza controllo dell'umidità. Inoltre, anche se sono state aggiunte alcune fasi di processo, l'intero processo ha migliori prestazioni consumando solo 0,14285 Kwh/kg invece di 0,158 Kwh/kg del processo tradizionale senza unità di disidratazione.
- Il controllo dell'umidità a monte della granulazione può eliminare il rischio di trasformazione di materiale inadatto, recuperandolo integro prima della trasformazione e permettendo di risparmiare materie prime. Il nuovo metodo può così consentire il pieno recupero dei rifiuti rendendoli perfettamente compatibili con il materiale vergine, grazie alla possibilità di omogeneizzare il gradiente dell'acqua con il relativo controllo di viscosità.
- Meno sprechi di additivi: gli additivi (stabilizzanti, lubrificanti, plastificanti, ritardanti di fiamma, catalizzatori in genere) sono i primi ad essere volatilizzati per problemi di essiccazione in caso di eccessiva deumidificazione e richiedono quindi un uso sovrabbondante e prudente. L'umidità equilibrata dei materiali permette di utilizzare solo la quantità strettamente necessaria di additivi. Diverse prove con miscele diverse hanno dimostrato una riduzione percentuale media del 30% nell'uso di additivi chimici, ottenendo prodotti di qualità perfetta con una grande omogeneità di granuli (deviazione standard di umidità: 1%). Considerando che per kg di materiale trattato in media 0,65 kg sono resine principali e 0,35 kg sono additivi e che 0,015 kg di questi ultimi sono additivi che possono essere salvati con il progetto fino al 35-40% (30% in media) ottenere 900 kg di utilizzo di additivi chimici risparmiati all'anno solo con l'impianto pilota in media.
RISULTATI ECONOMICO
L'approccio proposto è più economico di quello attuale. I principali risultati economici riguardano il valore economico diretto generato (circa il +10% stimato) raggiunto principalmente grazie alla riduzione dei costi energetici e all'aumento della produttività (meno sprechi) e dell'immagine aziendale sul mercato. Il minor costo di produzione è attestato a circa il 9%; considerando il miglioramento dell'immagine aziendale che influisce sul prezzo di vendita si può stimare un 10% di valore economico aggiunto.
I risultati del progetto sono stati divulgati alle parti interessate o potenzialmente tali, sia istituzionali che private, attraverso alcuni strumenti appositamente creati:
Roll Up
Board
- una sezione del sito web aziendale dedicata al progetto, regolarmente aggiornata, con strumenti scaricabili;
- l'aggiornamento della carta intestata aziendale con l'inserimento del logo LIFE+;
- la creazione di cartelloni con una breve descrizione degli obiettivi del progetto e del logo LIFE;
- creazione di materiale informativo (brochure, volantini) da distribuire in ogni occasione e su richiesta;
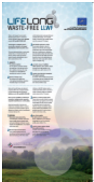
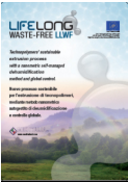
- creazione di materiale informativo (brochure, volantini) da distribuire in ogni occasione e su richiesta;
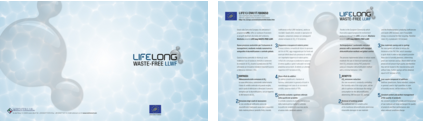
- partecipazione alle più importanti fiere mondiali di settore;
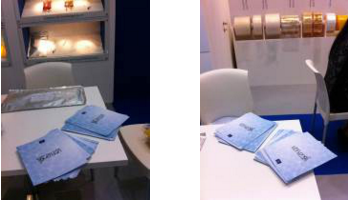
- pubblicazione di un articolo su una rivista specializzata del settore
- preparazione di un rapporto per non addetti ai lavori, comprendente materiale fotografico e una sintesi degli obiettivi e delle finalità;
- produzione di un materiale audiovisivo che illustri il funzionamento dell'impianto pilota;
- • organizzazione di un evento promozionale finale, nell'ultimo mese del progetto.
Le attività del progetto si sono presto concentrate sul sensore utilizzato per misurare l'umidità del materiale.
I sensori sono stati dimensionati, progettati e realizzati tenendo in considerazione i possibili materiali da trattare e i vari impianti da aggiornare.
Si è dovuto affrontare qualcosa di più per l'implementazione dei sensori nell'impianto, poiché la posizione di entrambi i sensori, la misurazione dell'umidità del materiale in ingresso e in uscita, richiedeva più attenzione di quanto ci si aspettasse. Il sensore era stato inizialmente installato vicino all'area in cui si muovono le pale di miscelazione e questo causava interferenze e distorsioni nel segnale, con conseguenti errori nelle misurazioni. Abbiamo quindi deciso di riposizionare i sensori, stabilendo che sarebbe utile installarne uno all'interno del turbo miscelatore per monitorare il contenuto di umidità durante la miscelazione delle materie prime ed eventualmente modificarne immediatamente i parametri di lavorazione per correggere eventuali anomalie. L'altro sensore, invece, misura la miscela secca all'interno del magazzino temporaneo durante la fase di avvio del ciclo.
Seguono le attività volte a realizzare la parte hardware dell'unità disidratante per garantire una corretta ed efficiente rimozione dell'acqua dal polimero, sulla base delle informazioni acquisite dalla rete sensoriale. L'applicazione di aria calda è stata così testata nel compound setacciato con il tempo di deumidificazione determinato, con buoni risultati, ma con il necessario arresto della produzione in continuo.
In alternativa al sistema off-line, quindi, l'azienda ha studiato la possibilità di gestire la deumidificazione ottimale all'interno del processo "in linea". Sono state così valutate tutte le variabili/cause della formazione e dello sviluppo di umidità all'interno del processo. La fonte principale è stata individuata nel turbocompressore del reattore dove l'incongruenza dei parametri (critica è la temperatura) provoca il continuo sviluppo di vapori e gas.
In particolare, il nuovo sistema è nato inserendo un circuito di raffreddamento all'interno del manicotto del turbomiscelatore del reattore, integrato con il processo di avvio ("start cycle") della preparazione dei compound. Poi, attraverso sensori disposti all'interno del reattore turbo-miscelatore manicotto è stato predisposto uno scambio con l'acqua che permetterebbe di portare la temperatura sempre nello stato di "avvio del sistema", evitando così che l'innalzamento della stessa temperatura porti allo sviluppo di umidità della miscela all'interno del reattore turbo-miscelatore.
Il composto è formato da una fase liquida e da una fase solida e viene polimerizzato per un ciclo di 15 minuti con una rampa di temperatura da 45 °C a 105 °C.
La combinazione di un sistema integrato tra il nuovo processo sopra descritto e il sensore posto a valle del buffer di accumulo ha reso possibile un sistema di produzione continuo con le condizioni ottimali di deumidificazione per raggiungere il processo desiderato.
CONTROL SYSTEM
DOWNSTREAM SENSOR
Il sistema è stato così validato con diversi test e messo in sicurezza attraverso i sensori realizzati che permettono di prevenire l'avvio del ciclo se non vengono rispettati i parametri critici di temperatura all'interno del turbocompressore e la percentuale di umidità residua.
Le seguenti attività miravano a fornire al nuovo sistema l'intelligenza di bordo necessaria per poter lavorare qualsiasi tipo di polimero in ingresso con qualsiasi tipo di contenuto di umidità.
Attraverso il sistema di controllo, la deumidificazione deve essere parametrizzata sulla base dei dati raccolti nel flusso di materie prime parametri fisico-chimici, alle condizioni ambientali per una risposta immediata ed una rimodulazione del ciclo di deumidificazione anche in funzione, appunto, delle caratteristiche delle materie prime in transito.
L'unità di controllo è stata implementata collegando il sistema di controllo del processo a quello che controlla la rete di sensori, realizzato specificatamente all'interno di processi di elaborazione e misura Meditalia e modificato per soddisfare il software di controllo comune per processi come quello Meditalia, per avere un unico sistema di controllo per l'intero processo. L'obiettivo era quello di aumentare le possibilità di diffusione della tecnologia realizzata e di contenere i costi applicativi e operativi, nonché, naturalmente, di ottimizzare al meglio il processo..
Il concetto base di funzionamento del nuovo processo si basa sul controllo della temperatura del turbo miscelatore e delle sequenze e dei tempi di ingresso dei componenti solidi e liquidi nel turbo miscelatore, modulati e controllati per garantire una produzione in costante garanzia di qualità. Le sonde sono state quindi inserite nel processo integrato con il software di produzione per garantire l'omogeneità del processo. Ogni processo è stato quindi personalizzato in base alle 5 famiglie di prodotti, modulando i tempi di ricevimento delle materie prime, i tempi di iniezione dei liquidi e controllando in modo adattivo la temperatura all'inizio e alla fine del ciclo di lavorazione all'interno del turbocompressore.
I cicli di lavoro determinati sono tutti documentati all'interno del programma sviluppato per la gestione delle miscele. Nei test sui materiali non correttamente essiccati, il parametro era misurabile direttamente sulla macchina e l'effetto era visibile a causa di continue ustioni e fermi macchina causati dall'eccesso di umidità.
Con l'impianto pilota, il materiale può essere messo in lavorazione il lunedì mattina e continuare senza interruzioni fino allo spegnimento il venerdì sera. Il risparmio di fermi dovuti alla continua combustione del materiale nel processo di estrusione ha permesso di ridurre sensibilmente gli scarti di processo e il tempo perso per le continue fermate e riavvii della linea di produzione.
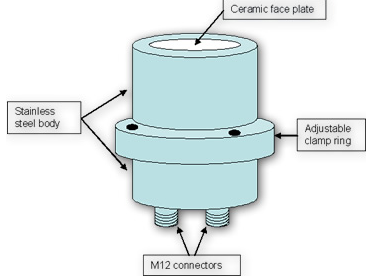
Si è dovuto affrontare qualcosa di più per l'implementazione dei sensori nell'impianto, poiché la posizione di entrambi i sensori, la misurazione dell'umidità del materiale in ingresso e in uscita, richiedeva più attenzione di quanto ci si aspettasse. Il sensore era stato inizialmente installato vicino all'area in cui si muovono le pale di miscelazione e questo causava interferenze e distorsioni nel segnale, con conseguenti errori nelle misurazioni. Abbiamo quindi deciso di riposizionare i sensori, stabilendo che sarebbe utile installarne uno all'interno del turbo miscelatore per monitorare il contenuto di umidità durante la miscelazione delle materie prime ed eventualmente modificarne immediatamente i parametri di lavorazione per correggere eventuali anomalie. L'altro sensore, invece, misura la miscela secca all'interno del magazzino temporaneo durante la fase di avvio del ciclo.
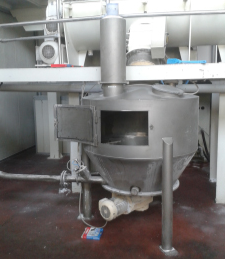
Seguono le attività volte a realizzare la parte hardware dell'unità disidratante per garantire una corretta ed efficiente rimozione dell'acqua dal polimero, sulla base delle informazioni acquisite dalla rete sensoriale. L'applicazione di aria calda è stata così testata nel compound setacciato con il tempo di deumidificazione determinato, con buoni risultati, ma con il necessario arresto della produzione in continuo.
In alternativa al sistema off-line, quindi, l'azienda ha studiato la possibilità di gestire la deumidificazione ottimale all'interno del processo "in linea". Sono state così valutate tutte le variabili/cause della formazione e dello sviluppo di umidità all'interno del processo. La fonte principale è stata individuata nel turbocompressore del reattore dove l'incongruenza dei parametri (critica è la temperatura) provoca il continuo sviluppo di vapori e gas.
In particolare, il nuovo sistema è nato inserendo un circuito di raffreddamento all'interno del manicotto del turbomiscelatore del reattore, integrato con il processo di avvio ("start cycle") della preparazione dei compound. Poi, attraverso sensori disposti all'interno del reattore turbo-miscelatore manicotto è stato predisposto uno scambio con l'acqua che permetterebbe di portare la temperatura sempre nello stato di "avvio del sistema", evitando così che l'innalzamento della stessa temperatura porti allo sviluppo di umidità della miscela all'interno del reattore turbo-miscelatore.
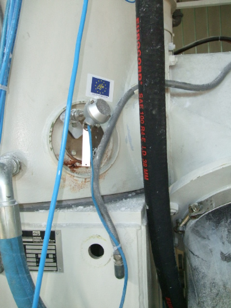
Il composto è formato da una fase liquida e da una fase solida e viene polimerizzato per un ciclo di 15 minuti con una rampa di temperatura da 45 °C a 105 °C.
La combinazione di un sistema integrato tra il nuovo processo sopra descritto e il sensore posto a valle del buffer di accumulo ha reso possibile un sistema di produzione continuo con le condizioni ottimali di deumidificazione per raggiungere il processo desiderato.
CONTROL SYSTEM
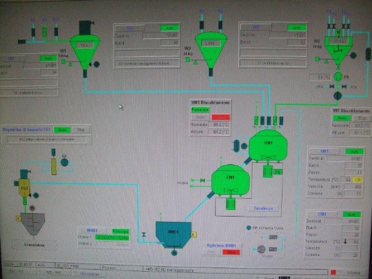

Il sistema è stato così validato con diversi test e messo in sicurezza attraverso i sensori realizzati che permettono di prevenire l'avvio del ciclo se non vengono rispettati i parametri critici di temperatura all'interno del turbocompressore e la percentuale di umidità residua.
Le seguenti attività miravano a fornire al nuovo sistema l'intelligenza di bordo necessaria per poter lavorare qualsiasi tipo di polimero in ingresso con qualsiasi tipo di contenuto di umidità.
Attraverso il sistema di controllo, la deumidificazione deve essere parametrizzata sulla base dei dati raccolti nel flusso di materie prime parametri fisico-chimici, alle condizioni ambientali per una risposta immediata ed una rimodulazione del ciclo di deumidificazione anche in funzione, appunto, delle caratteristiche delle materie prime in transito.
L'unità di controllo è stata implementata collegando il sistema di controllo del processo a quello che controlla la rete di sensori, realizzato specificatamente all'interno di processi di elaborazione e misura Meditalia e modificato per soddisfare il software di controllo comune per processi come quello Meditalia, per avere un unico sistema di controllo per l'intero processo. L'obiettivo era quello di aumentare le possibilità di diffusione della tecnologia realizzata e di contenere i costi applicativi e operativi, nonché, naturalmente, di ottimizzare al meglio il processo..
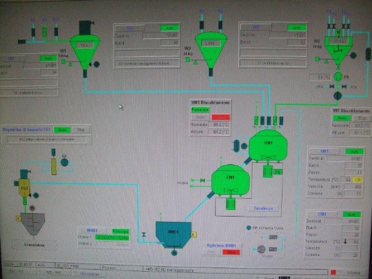
Il concetto base di funzionamento del nuovo processo si basa sul controllo della temperatura del turbo miscelatore e delle sequenze e dei tempi di ingresso dei componenti solidi e liquidi nel turbo miscelatore, modulati e controllati per garantire una produzione in costante garanzia di qualità. Le sonde sono state quindi inserite nel processo integrato con il software di produzione per garantire l'omogeneità del processo. Ogni processo è stato quindi personalizzato in base alle 5 famiglie di prodotti, modulando i tempi di ricevimento delle materie prime, i tempi di iniezione dei liquidi e controllando in modo adattivo la temperatura all'inizio e alla fine del ciclo di lavorazione all'interno del turbocompressore.
I cicli di lavoro determinati sono tutti documentati all'interno del programma sviluppato per la gestione delle miscele. Nei test sui materiali non correttamente essiccati, il parametro era misurabile direttamente sulla macchina e l'effetto era visibile a causa di continue ustioni e fermi macchina causati dall'eccesso di umidità.
Con l'impianto pilota, il materiale può essere messo in lavorazione il lunedì mattina e continuare senza interruzioni fino allo spegnimento il venerdì sera. Il risparmio di fermi dovuti alla continua combustione del materiale nel processo di estrusione ha permesso di ridurre sensibilmente gli scarti di processo e il tempo perso per le continue fermate e riavvii della linea di produzione.